| Japan |
We often hear about the differences between American and Japanese work cultures. For example, Japanese business people tend to be very subtle when expressing opinions, often relying on non-verbal communication, assuming that others will understand their meaning. And unlike individualistic thinking Americans, Japanese workers typically conform to group consensus, seeking to create harmony rather than call attention to one’s self.
Ed Katz, “Preacher Ed” of the International Office Moving Institute (IOMI®) experienced these differences firsthand as he introduced IOMI® to Japan at the request of one of that country’s most successful office movers.
From May 15-19, 2017, the self-proclaimed, self-ordained “minister of office moving” delivered several speeches in Tokyo, Hamamatsu, and Shin Osaka, and presented at the world headquarters of Kaneka, a $5+ billion diversified company with global locations.
Ed showed the Japanese movers how IOMI® teaches the moving industry to estimate office moves accurately by using a scientifically based man-hour formula instead of the traditional household goods’ “cube and pounds” method, which amounts to little more than a coin toss guesstimate.
And while the Japanese are obsessed with providing excellent customer service and delivering exceptional results, it was clear from the question-and-answer sessions after each presentation that there are certain realities that must be considered when doing business in Japan. Here are a few examples:
Land & Square Foot Costs – Slightly smaller in area than California, Japan squeezes 100 million people into a country that’s 5% (1/20th) the size of the US, which means that undeveloped land doesn’t exist and the price per square foot is outrageously expensive. IOMI®’s floating method calls for leaving furniture on dollies on the floor of the truck until ready to be moved. Unfortunately, with land and warehouse space so expensive in Japan, office movers there say they can’t afford to store the hundreds of extra dollies required to implement the floating method. Therefore, they end up placing furniture on dollies to load them into the truck, then removing the dollies and re-placing furniture on dollies at the destination. This ‘double handling’ approach takes more time and increases the risk of damage as well as worker injuries.
Use of Part-Time Employees – Japanese movers always use full-time employees with high skill and experience levels. So even when business is slow, these workers are still on the payroll.
No Bucket Brigades – Unlike American movers, who pass furniture down (or up) the line in the placement of their moving crews, in Japan, whoever places the furniture on the dolly pushes it all the way onto the truck and sets it in place. Without criticizing their methods, Ed gently pointed out that the IOMI® bucket brigade method enables supervisors to measure productivity so they can better manage and supervise crews. For example, with the IOMI® bucket brigade, if a crew member is not working as fast and efficiently as the rest of the crew, it becomes readily apparent because the furniture stalls or backs up. Without the bucket brigade, each employee works at his own pace, which could interfere with group productivity. Ed pointed out that “slackers” pull the rest of the crew down to their level and that if everyone is being paid the same wage regardless of level of effort, where is the motivation to work at maximum productivity. Of course this is where cultural differences really come to the surface: Japanese workers are dedicated to the success of the group vs. the individual, so many would probably find it inconceivable to think about a co-worker as a ‘slacker.’
Carpet & Floor Protection – No movers in Japan use Masonite® or carpet mask, preferring Polynite® for floor protection. Unlike the competition that has a similar product, only Polynite® is guaranteed not to curl, bow, or bend after it’s installed. Such bending or curling could cause a mover or the client’s employee to trip and fall over the raised section causing a worker’s comp claim.
Processing Times – Japanese workers spend more time processing their work than do American workers and often that’s simply because Japanese companies and their leaders are reluctant to change. Such attitudes can make it difficult to introduce new methods, even if they will bring about greater efficiency.
Sense of Humor – Last but not least, nobody in Japan thought that Ed Katz was funny. No one laughed at his silly jokes and humor. The Japanese are very focused and serious people. It’s a good thing that he’s 72-years-old because their lack of appreciation for his antics sailed right over his head.
Despite these obvious cultural differences, Ed’s trip was a success on many levels. And while adopting IOMI®’s methods may take time in Japan, in the end the goals are the same: provide clients with the best possible service and customer experience, minimize risk to furniture, and decrease worker injury. Those are goals that translate well into ANY language!
Here are some fun photos from Ed’s Asian tour!
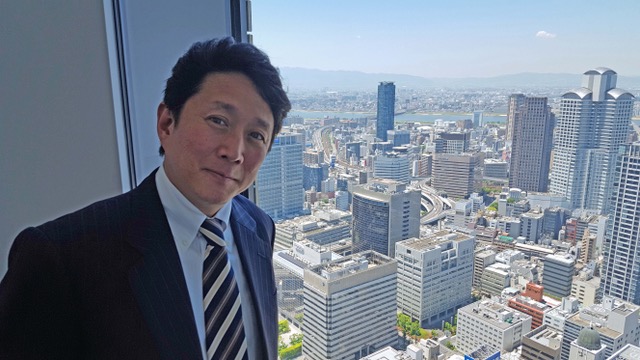
Henry Masuda, Polynite® sales executive and Ed’s interpreter.
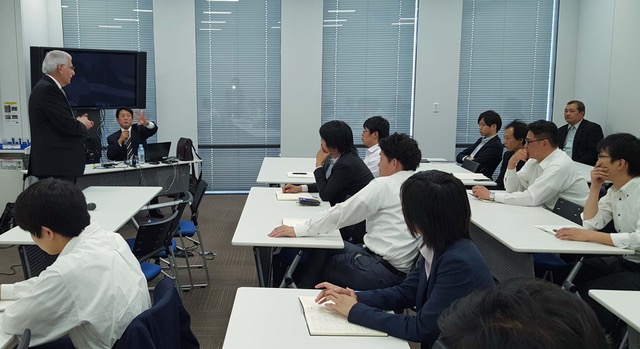
Ed presented at Kaneka, a $5 billion diversified company, at their world headquarters in Osaka, Japan.
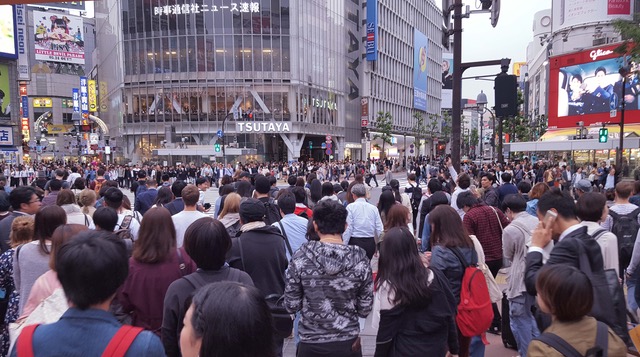
Japan has 100 million people in a country that’s smaller than California. When the crosswalk light turned from red to green, this is what we experienced!
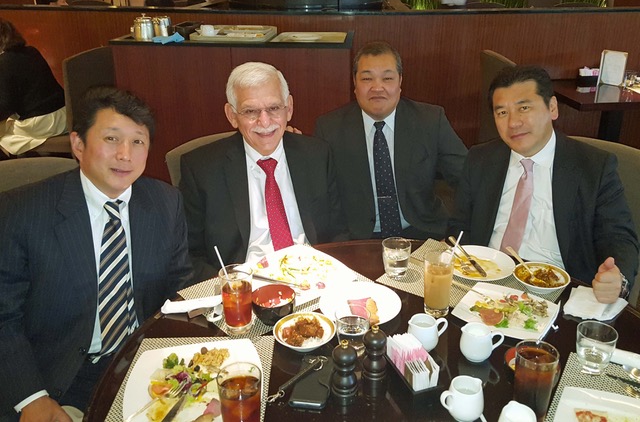
(L-R) Henry Motohisa Masuda, Sanvic, Inc., Sales Executive and interpreter; Ed Katz, IOMI®; Motokazu Miwa, President, Sanvic, Inc.; Etsuo Yoshiike, Division Manager, Kaneka.
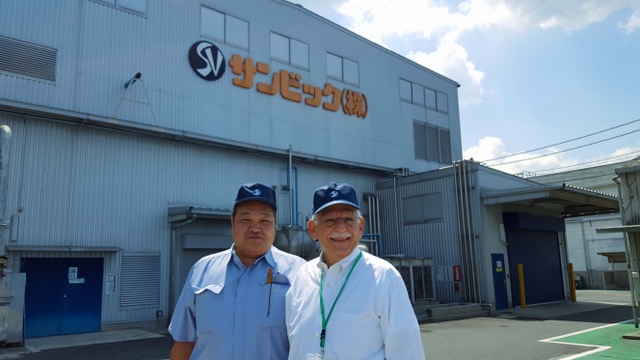
While in Japan, Ed toured the plant where Polynite® is manufactured.
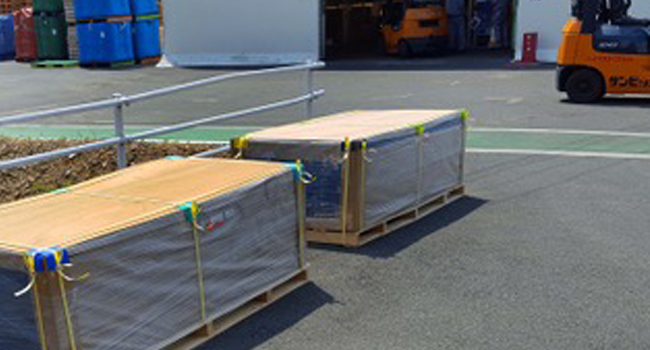
So many pallets of Polynite® were being prepared for shipping that they had to temporarily stage many outside.
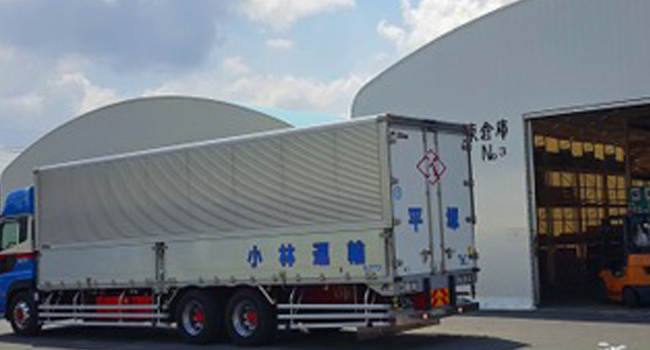
In the short time that Ed was touring the Polynite® plant, trucks were backed up loading Polynite® to be distributed all over the US, Japan, and now Europe.
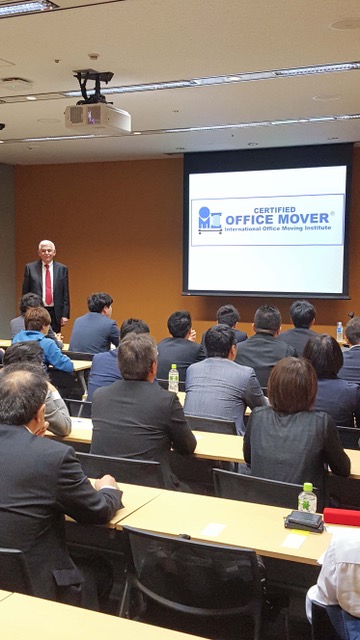
During the “Q & A” session, Ed learned that his Japanese students were surprised American movers use Masonite® or carpet mask. They prefer Polynite® to protect floors during a move.
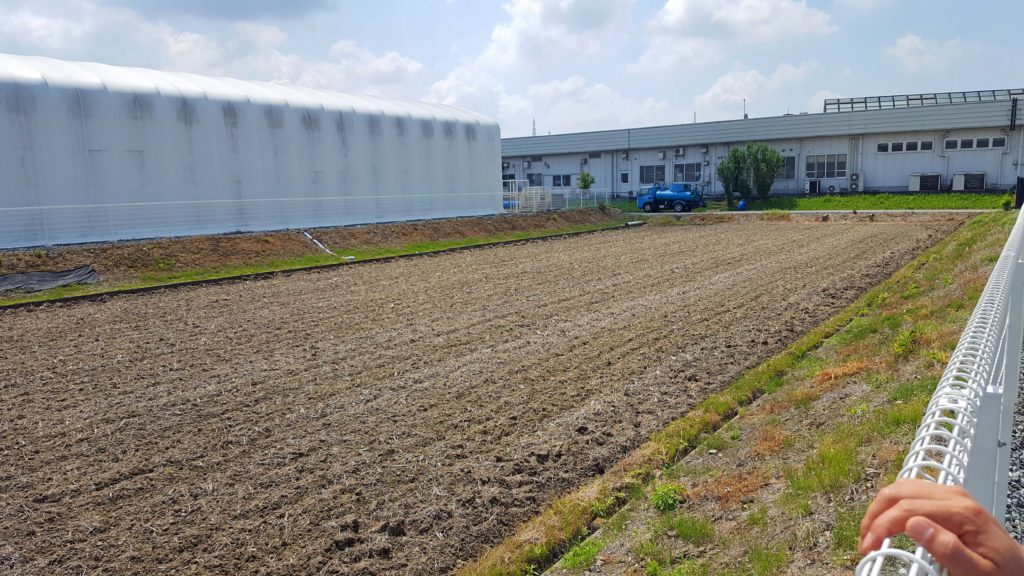
In Japan, every square inch of space is used for productive means. Right next to the Polynite® factory was a newly seeded rice paddy.
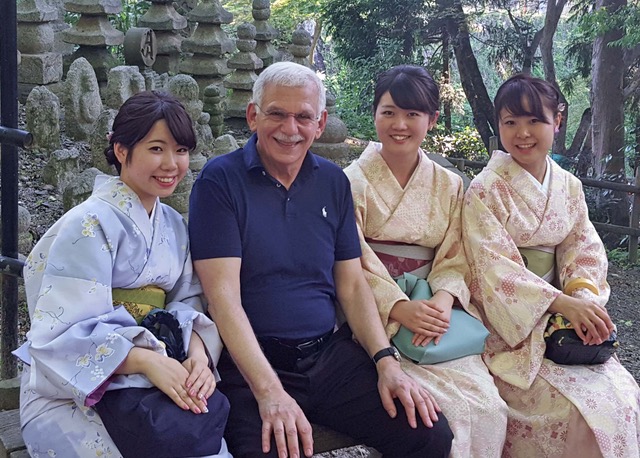
There is a least one shrine or temple in every Japanese city. Ed tried to “recruit” students for his office moving seminar at this famous Buddhist temple.
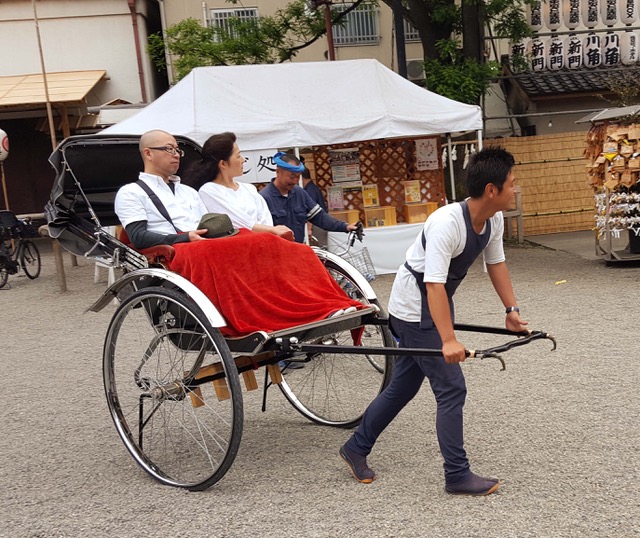
With road space at a premium, public transportation takes many forms.
The International Office Moving Institute (IOMI®) is not an alliance, a trade association, or a moving company, but an independent, unbiased office moving resource and training organization beholden to no one. We accept no advertising. The links from within our pages to other web sites are reciprocal.
For more than a decade, many in the moving industry and companies planning a move have come to rely on officemoves.com as a steadfast source of best practices. We advocate, and through the International Office Moving Institute (IOMI®), teach:
• Minimizing the risk of damage to walls, floors, doors and elevators during your move. IOMI® Certified Office Movers® and Certified Project Managers® learn the best practice methods for installing extensive building protection.
• Minimizing the risk of damage to furniture and computers during your move. IOMI® Certified Office Movers® and Certified Project Managers® learn the best-practice methods for wrapping every monitor, printer, CPU, server, and copier with two layers of anti-static bubble wrap (with the bubbles facing the bubbles) instead of pad-wrapping computers with filthy furniture pads.
• Timing is of the essence on your office move. If your mover doesn’t finish the job on time, it can cost your company thousands of dollars of nonproductive downtime. IOMI® Certified Office Movers® and Certified Project Managers® learn an estimating formula that’s based upon man-hours instead of the unreliable method typically used on household moves that’s based on weight.
The IOMI® proprietary estimating formula is uncannily accurate because it factors in not only volume but the unique logistics of both the building you’re moving from and to.
Why hire an IOMI®
Certified Office Mover®?
1. On time for the price quoted
One of the biggest complaints about movers is that they often badly underestimate the cost of a move and then don’t finish on time. An International Office Moving Institute (IOMI®)-trained mover learns a formula for accurately estimating cost. By calculating the number of trucks and movers for how long, IOMI® Certified Office Movers® can base estimates on man-hours, volume, and logistics, and not weight, which household movers typically use when quoting an office move. As a result, the chances of a move completing on time for the price quoted is greatly improved.
2. Minimize risk of damage
IOMI® Certified Office Movers® learn the latest techniques to minimize risk of damage to furniture and computers, and are trained in extensive building protection to minimize risk of damage to carpet, walls, doors, and door jambs.
3. Minimize downtime
There is a better way! IOMI® Certified Office Movers® understand that their customers can’t afford to shut down operations during a move, and are trained in techniques to keep client employees working. Many IOMI® graduates offer the “boxless” move — moving the contents in the furniture instead of the contents and the furniture.
Learn More About Becoming An
IOMI® Certified Office Mover®
Call 404-358-2172